Resistance Welding
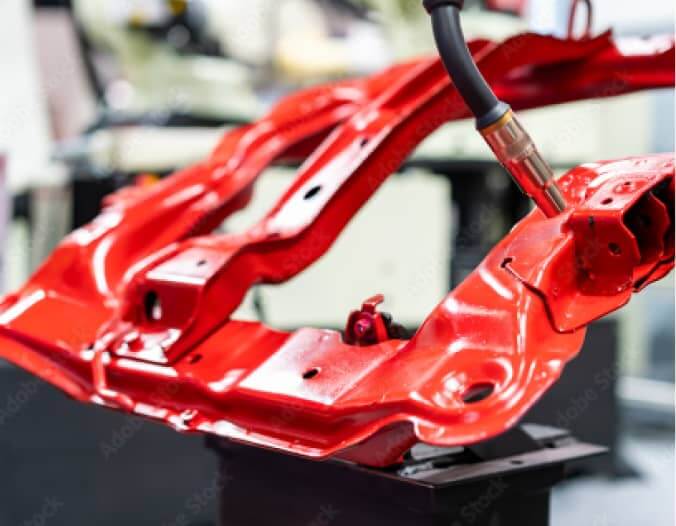
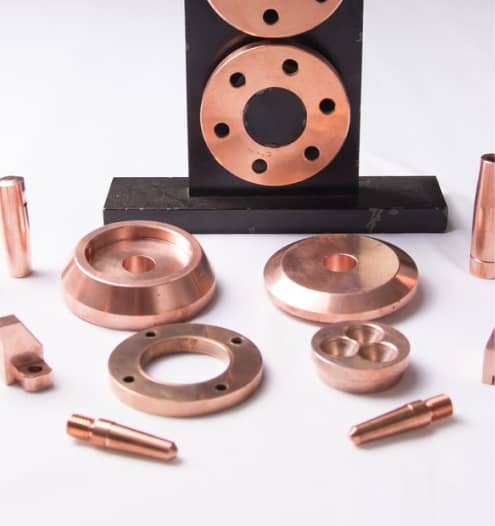
Resistance welding is a welding technology widely used in the manufacturing industry for joining metal sheets and components. The weld is generated by passing a strong current through the metal sheet combination. Hence, the workpieces are heated to such an extent that they melt at the welding point and join together. The main benefit of resistance welding is that no additional materials are required to form the bond. This makes the process very economical.
There are several different methods to be distinguished. Generally, resistance welding is divided into fusion welding and pressure welding. The latter works by exerting a pressing force between the workpieces to be welded, while the former uses filler materials.
The various processes differ – sometimes more, sometimes less – from each other. At the same time, each one is unique and may need special resistance welding components. Some of the best-known processes are listed below:
What is spot welding?
Resistance spot welding is one of the most frequently used pressure welding processes. It works entirely without shielding gas and any filler materials, making the process comparably simple. An electric current is passed through an electrode to generate heat. In combination with the applied pressure, the contact points melt, and a welding lens is formed. As the current is turned off, the material cools and solidifies, creating a stable connection.
Spot welding electrodes with a high copper content are ideal for welding high-resistance materials such as stainless steel, monel metal, and nichrome. That is why we suggest using AMCOLOY® 88, AMPCOLOY® 89, AMPCOLOY® 91, AMPCOLOY® 95, and AMPCOLOY® 940. Please contact our expert if you want to know, which alloy is the best choice for your application.
What is resistance seam welding?
Resistance seam welding is a subset of resistance spot welding using wheel-shaped electrodes instead of regular electrodes. The difference is that the workpiece rolls between the wheel-shaped electrodes while weld current is applied. Depending on the weld current and welding time settings, the weld created may overlap, forming a complete welded seam, or may simply be individual spot welds at defined intervals.
For welding mild steel and carbon steel, we highly suggest welding wheels made of AMPCOLOY® 972 and AMPCOLOY® 940. For welding stainless steel, we suggest using AMPCOLOY® 95.
What is projection welding?
In projection welding, the electrodes are made of flat copper plates. The current flows through small, prefabricated projections in the sheet metal or component. For this purpose, one or more welding projections are made in one of two workpieces to be joined. These welding projections are special elevations that protrude from the workpiece. The preformed projection softens and collapses during welding, resulting in a high-quality weld.
Materials used for projection welding should have RWMA class 4. We suggest using AMPCOLOY® 83 or AMPCOLOY® 944, which both offer extremely high hardness and compressive strength.
What is mesh welding?
Mesh welding is a special form of projection welding. The welding projections are not specially constructed for the welding process but are already part of the natural geometry of the components. Metal grids are an example of this process.
As the electrode for cross-wire welding needs high hardness and strength, we recommend using AMPCOLOY® 95.
What is resistance butt welding?
In this process, workpieces with the same cross-section are clamped with the electrodes, and the butt ends are joined together. Under pressure, the current is passed through the electrodes and the workpieces through the abutting surfaces. The workpieces are joined together with the heat generated by the electrical resistance. This process is mainly used for welding small parts such as metal wires, strips, and rods.
We highly recommend using AMPCOLOY® 83 as electrode material. AMPCOLOY® 95 can be used as a substitute when another alloy cannot be used due to manufacturing reasons of the electrode.
How to reduce weld spatter
Weld spatters are annoying but, unfortunately, part of everyday life in welding. As they negatively influence productivity and may even lead to downtimes, you want to minimize weld spatters as much as possible. Many factors can cause weld spatters, such as the materials involved in the welding process, the used filler metal, the welding setting itself, and whether shielding gas is used or not.
Hence, there is a lot to consider when it comes to avoiding weld spatter in the best way possible. For instance, using the right high-quality filler metal that fits the task can have a huge impact. Our welding wire selection guide helps you find the correct filler metal. There are a lot of other useful tips to minimize weld spatter.
AMPCO METAL Resistance welding components
Due to its high speed and reliability, resistance welding is well-suited to mass production across various industries, including white goods, automotive, heating and ventilation, aerospace, and construction. AMPCO METAL has developed a wide range of high copper alloys that are well suited for several applications in the process of resistance welding as well as dealing with weld spatter:
Here are some typical uses where our alloys can make a significant impact on your resistance welding processes:
- For clamping element, we suggest the use of AMPCOLOY® 83 and AMPCOLOY® 944 due to their high resistance to any sort of weld spatter.
- For CuCrZr plates in spot welding, we suggest AMPCOLOY® 972 for a more than four times higher life span than regular plates.
- For robotic MIG / MAG welding nozzles, we suggest AMPCOLOY® Nozcap for unmatched resistance to weld spatter.
- For spot and seam welding electrodes, we suggest AMPCOLOY® 95, AMPCOLOY® 940, and AMPCOLOY® 972 for smooth functionality under elevated operating temperatures.